Introduction
In industrial settings where hazardous conditions are prevalent, ensuring the safety and reliability of electrical systems is of utmost importance. Shielded cables play a crucial role in protecting both personnel and equipment from the risks associated with electromagnetic interference (EMI), radio frequency interference (RFI), and other external factors that can compromise the performance of electrical systems. This article explores the significance of shielded cables in hazardous environments, their construction, applications, and best practices for installation and maintenance.
Understanding Shielded Cables
Shielded cables are specially designed electrical cables that incorporate a protective layer to shield against external electromagnetic interference and radio frequency interference. These cables are commonly used in environments where EMI and RFI are present, such as industrial facilities, power plants, chemical plants, and oil refineries. The shielding layer acts as a barrier, preventing external signals from disrupting the transmission of electrical signals within the cable.
Construction of Shielded Cables
Shielded cables consist of several components that work together to provide protection against interference. The key components of a shielded cable include:
1. Conductor: The conductor is the core component of the cable that carries the electrical current. It is typically made of copper or aluminum, which are good conductors of electricity.
2. Insulation: The insulation layer surrounds the conductor and provides electrical insulation to prevent short circuits or electrical faults. Common insulation materials include PVC (Polyvinyl Chloride), XLPE (Cross-Linked Polyethylene), and EPDM (Ethylene Propylene Diene Monomer).
3. Shielding: The shielding layer is the critical component that protects the cable from external interference. The shield can be made of various materials, such as aluminum foil, copper tape, or a combination of both. The shield is grounded to dissipate any unwanted signals that may be picked up by the cable.
4. Jacket: The outer jacket provides mechanical protection to the cable and ensures durability in harsh environments. The jacket material is chosen based on the specific application requirements, such as resistance to chemicals, abrasion, or extreme temperatures.
Types of Shielded Cables
There are several types of shielded cables available, each designed for specific applications and environmental conditions. Some common types of shielded cables include:
1. Foil Shielded Cable: This type of cable consists of a thin layer of aluminum foil wrapped around the conductor, providing effective shielding against EMI and RFI.
2. Braided Shielded Cable: Braided shielded cables use a woven mesh of copper or aluminum wires to provide enhanced protection against interference. The braided shield offers higher flexibility and durability compared to foil shielding.
3. Combination Shielded Cable: Combination shielded cables combine both foil and braided shielding for maximum protection against external interference. These cables are ideal for high-risk environments where multiple sources of interference are present.
Applications of Shielded Cables in Hazardous Environments
Shielded cables are widely used in hazardous environments where electrical systems are exposed to EMI, RFI, and other external factors that can disrupt signal transmission. https://www.jiangyuancables.com/pvc-insulated-sheathed-control-cable/ of shielded cables in hazardous environments include:
1. Industrial Automation: In industrial automation systems, shielded cables are used to connect sensors, actuators, and control devices to ensure reliable communication and data transmission in harsh industrial environments.
2. Power Distribution: Shielded cables are essential for power distribution systems in hazardous environments, such as power plants and substations, where electrical interference can lead to equipment malfunctions or safety hazards.
3. Communication Networks: Shielded cables play a vital role in communication networks, including data centers, telecommunications facilities, and industrial Ethernet systems, where reliable signal transmission is critical for network performance.
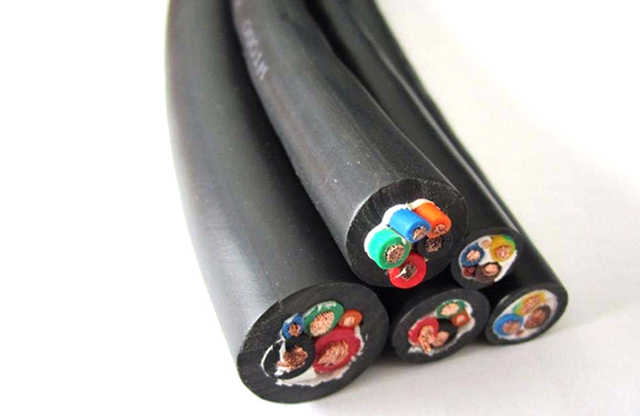
4. Process Control Systems: In chemical plants, oil refineries, and other process industries, shielded cables are used in process control systems to monitor and control various operations, ensuring the safety and efficiency of industrial processes.
Best Practices for Installation of Shielded Cables
Proper installation of shielded cables is essential to ensure optimal performance and reliability in hazardous environments. To achieve the best results, the following best practices should be followed during the installation of shielded cables:
1. Maintain Proper Grounding: The shielding layer of the cable should be properly grounded to dissipate unwanted signals and prevent electromagnetic interference. Grounding connections should be secure and follow industry standards to minimize the risk of electrical faults.
2. Avoid Cable Damage: Care should be taken to avoid damaging the shielding layer or insulation during installation. Sharp bends, excessive tension, or mechanical stress can compromise the integrity of the cable and reduce its effectiveness in shielding against interference.
3. Minimize Cable Length: Keeping cable lengths as short as possible helps reduce the risk of signal degradation and interference. Using the appropriate cable length for the application minimizes the chances of signal loss and ensures reliable transmission.
4. Separate Power and Data Cables: To prevent interference between power and data signals, it is recommended to separate power cables from shielded data cables. Crossing power and data cables can introduce noise and disrupt signal integrity.
5. Use Cable Management Systems: Proper cable management systems, such as cable trays, conduits, and cable ties, should be used to organize and protect shielded cables from environmental hazards, such as moisture, chemicals, and mechanical damage.
Maintenance and Troubleshooting of Shielded Cables
Regular maintenance and inspection of shielded cables are essential to identify potential issues and prevent system failures in hazardous environments. Some key maintenance practices for shielded cables include:
1. Visual Inspection: Conduct regular visual inspections of shielded cables to check for signs of wear, damage, or corrosion. Look for exposed shielding, cracks in the insulation, or loose connections that may compromise the cable's effectiveness.
2. Testing Shielding Integrity: Use specialized testing equipment, such as a multimeter or cable tester, to verify the integrity of the shielding layer. Check for continuity and proper grounding to ensure that the shield is effectively protecting the cable from interference.
3. Environmental Monitoring: Monitor environmental conditions, such as temperature, humidity, and exposure to chemicals, that can impact the performance of shielded cables. Take preventive measures to protect cables from adverse conditions that may lead to degradation or failure.
4. Troubleshooting Interference Issues: In case of signal interference or communication disruptions, troubleshoot the system to identify the source of the problem. Check for nearby sources of electromagnetic interference, faulty grounding, or improper cable installation that may be causing the issue.
Conclusion
Shielded cables play a critical role in ensuring the safety and reliability of electrical systems in hazardous environments. By providing protection against electromagnetic interference and radio frequency interference, shielded cables help maintain the integrity of signal transmission and prevent system failures in industrial settings. Understanding the construction, types, applications, and best practices for installation and maintenance of shielded cables is essential for creating a secure and efficient electrical infrastructure in hazardous environments. By following industry standards and implementing proper safeguards, organizations can mitigate risks and ensure the optimal performance of electrical systems in challenging industrial environments.